Micro-Scale Biogas Production: A Beginners Guide
By Rich Dana, NCAT Agriculture Specialist
Abstract
Anaerobic digestion is a simple biochemical process by which waste products can be converted to energy. Using manure, plant waste, crop residue, food scraps, or other waste products, farmers can reduce their dependence on fossil fuels while saving money, reducing greenhouse gas emissions, and solving odor problems (not to mention producing high-quality compost fertilizer as a by-product). This publication provides a beginners guide to using anaerobic digestion to produce usable biogas on a small scale with a minimal investment.
For more information on biogas and a discussion of larger-scale, manure-based digesters for livestock operations, see the ATTRA publication Anaerobic Digestion of Animal Wastes: Factors to Consider.
Contents
Introduction
Using the Gas
Small is Beautiful
Biogas Basics: The Chemistry of Anaerobic Digestion
Feeding Your Digester
Micro-Digester Designs
Start-Up, Operation, and Maintenance
Side Streams
Conclusion
References
Introduction
Anaerobic digestion is one of the most basic processes of life on earth. Anaerobic means “in the absence of oxygen” and anaerobic digestion takes place when biodegradable matter decomposes in a closed environment. By managing the digestion process and capturing the biogas produced, we can power boilers, burners, and generators, and possibly even refrigerators.
In the United States, there is a great deal of interest in using large-scale anaerobic digesters to control odor at livestock facilities and burning the biogas produced to run electrical generators. Commonly referred to as methane digesters, these large-scale units actually digest manure and produce biogas, which is made up of carbon dioxide (CO2) and methane (CH4) with smaller amounts of water vapor (H2O), hydrogen sulfide (H2S), and in some cases ammonia (NH3). Methane is flammable gas that can be used to make power and is the primary component of the fossil fuel natural gas, commonly used to heat homes.
Although not widely used in the United States, small-scale digesters are used successfully all over the world to turn small amounts of manure, plant waste, and food scraps into usable energy. For hundreds of years, biogas has been used in China and India (and more recently in Africa and Central America) to provide gas for cooking, heating, and lighting, utilizing very simple, low-tech designs. This publication will examine several of the common designs for building micro-digesters that have been developed around the world and discuss how sustainable farmers in American can take a lesson from their counterparts in the developing world.
Disclaimer: This publication is meant as an introduction to micro-scale biogas production, and not a complete hands-on manual on how to construct and operate a digester. There is a list of references at the end of this publication, and we suggest doing considerable additional research before committing time and resources to a biogas project. Most importantly, remember that biogas, though relatively safe, can be dangerous, flammable, and potentially explosive if handled improperly. We suggest that you exercise all possible safety precautions and abide by all local, state, and federal laws that might apply to a digester project in your location.
Using the Gas
If you decide to build the digester, how will you use the gas? Biogas can take the place of propane or natural gas in many instances. The most common use is for cooking. It can, of course, be used as a heat source as well — to supplement home heating, for heating a poultry house, farrowing house incubator or other small livestock building, or for heating a greenhouse.
One unique use that has not been widely explored in the U.S. (but has in China) is using the gas to power an absorption refrigerator. This is a type of refrigerator that uses a propane flame rather than an electric compressor to create the evaporative cooling cycle. These refrigerators are commonly found in RVs and in locations that have no electricity or unreliable electricity supplies. Though there is little research available on the use of methane to power absorptive cooling, methane has potential for use by farmers who may be looking for refrigeration options in remote areas.
Small is Beautiful
There are several major technical issues to overcome in order to operate a large-scale digester successfully and use it to generate wholesale electricity. Maintaining proper bacterial health in a 40,000- to multi-million-gallon digester tank can be difficult—and mistakes are expensive. Large-scale digesters require hundreds—or thousands—of head of livestock to provide adequate manure, creating material handling issues. In order to run large, sensitive electrical generating equipment, the biogas must be “scrubbed” to remove most of the other gases, which can add work and expense. Large digesters often require a full-time manager. On the other hand, a microdigester can supply a family with cooking gas for two meals a day (or add heat to a greenhouse or workshop), from the manure of a few pigs, cows, or chickens, or food scraps and rotten or unusable vegetables and fruit. Because the cost of construction is low, the feedstock is free, and the fuel is used at the source, economic risk can be minimized and sustainability maximized.
In other parts of the world where energy resources are not as readily available as they are in the United States, the micro-digester is an important technology because of its low cost (and the ability to adapt salvage materials or materials that are commonly at hand), simplicity, and environmental and health benefits. In places where wood is used for cooking and heating, deforestation is a major concern and burning wood can cause air quality issues and respiratory problems for residents—especially small children. A household digester can reduce the work of gathering wood and provide a cheap and plentiful fuel source where before there was none.
Biogas Basics: The Chemistry of Anaerobic Digestion
Anaerobic bacteria and archaea predate most other forms of life on our planet, having developed in the period when the earth’s atmosphere was mainly methane (CH4), carbon dioxide (CO2), and water vapor (H2O). Anaerobic digestion takes place in environments with limited oxygen: underwater in a swamp or marsh, at the bottom of a compost heap, or in the gut of animals. Anaerobic digestion is used in septic systems and sewage treatment plants to break down waste.
The Stages of Anaerobic Digestion
There are four stages to the digestion process—hydrolysis, acidogenesis, acetogenesis, and methanogenesis. These stages need to be managed early on in starting a digester, but if the process is properly maintained, methane production should require a minimum of chemical testing and treatment. Bacteria must do their work in the earlier stages to use up the oxygen in the material, and then break it down into volatile fatty acids and fermented alcohols, before the methanogenic bacteria can start to make methane. The process is as follows:
- Hydrolysis: Enzymes break down and liquefy the smaller molecules and break down large polymers in the material.
- Acidogenesis: The products of the hydrolysis (soluble monomers) are fermented to volatile fatty acids (or VFAs) and alcohols.
- Acetogenesis: Acetogenic bacteria break down the VFAs and alcohols, acetic acid, carbon dioxide, and hydrogen.
- Methanogenesis: The methanogenic bacteria convert acetic acid and hydrogen into CO2 and methane. (Note: The three earlier stages can take place at lower temperatures than Methanogenesis.)
Temperature and pH
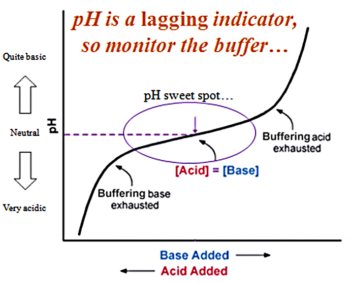
Figure 1. Graphic: David House
Two of the most important factors for proper anaerobic digestion and methane production are temperature and pH. Failure to regulate these two factors is among the most common problems with a digester.
Most anaerobic bacteria perform best in warmer atmospheres. This is why micro-digesters are most common in areas closer to the equator. This does not mean a micro-digester will not function in more northerly climates, but it does affect design decisions, as the digester may need to be insulated or even heated to make large amounts of methane. Anaerobic digestion does not stop completely at lower temperatures, but methanogenesis is the stage most seriously hindered by low temperatures, and this will reduce methane production. There is evidence, however, that plant-based feedstocks may perform better at low temperatures than do manure-based systems (House, 2006).
Although micro-digesters in Central America or India often operate completely without added heat or even insulation at temperatures ranging from 60 degrees Fahrenheit to over 100 degrees Fahrenheit, the micro-digester design most popular in China is an underground design, which utilizes the earth’s geothermal properties to maintain a healthy temperature. This publication discusses design considerations below, in the section entitled Micro-Digester Designs: Global D.I.Y. technology.
Along with temperature, pH is vital to digester health. The pH is a measure of the acidity or alkalinity (baseness) of the contents of the digester. Just as in the human digestive system, too much acid creates “indigestion” in the anaerobic system.
Pure water is said to be neutral, with a pH level of about 7. Acids have pH numbers below 7, while bases have numbers above 7. A digester operates best near the neutral point, up to a pH of about 8.5. In the early stages of the anaerobic process, when the digester is making acids, the pH can drop to 6 or below. When it reaches methanogenesis, it will operate in the 7.5 to 8.5 range.
It is important to remember that the pH level becomes less of an issue when the digester is well-buffered, as it can take a certain amount of acid or base material being added to it without upsetting the digestion (Fry, 1973). Buffering is the digester’s ability to resist pH change. Since pH is a “lagging indicator,” proper buffering is important to avoid problems with acidity (see Figure 1).
In a large-scale digester, large variations in pH can be catastrophic. In a micro-digester, however, high or low pH conditions may be corrected relatively simply. A high-acid condition can be treated with small amounts of lime, ammonia, or even bicarbonates like baking soda.
Carbon/Nitrogen Ratio (C:N)
Carbon and nitrogen are the two components that anaerobic bacteria require for survival. They need about 30 times more carbon than nitrogen, so the C:N ratio of your substrate should be about 30:1. This is important when formulating your slurry. When determining the C:N ratio of feedstock like manure, the animal feed and amount of bedding material can heavily affect the actual amounts of carbon and nitrogen—you will need to adjust your feedstock accordingly (see Table 1).
Table 1: Carbon Nitrogen Ratio | |
Substance | C:N |
Cow Manure—Alfalfa | 16:01 |
Cow Manure—Dairy (with bedding) | 21:01 |
Pig Manure | 14:01 |
Sheep Manure | 20:01 |
Chicken Manure | 15:01 |
Oat Straw | 48:01:00 |
Turnip Tops | 19:01 |
Corn Stalks | 53:01:00 |
Grass Clippings | 19:01 |
Sunflower | 30:01:00 |
Source: House, David. 2006. Biogas Handbook. p. 37-40. |
Feeding Your Digester: Substrates
In the proper feeding and care of your digester, you must remember the “Seven Ss” of anaerobic digester design (see Table 2):
Table 2: The Seven Ss of Digester Design |
1. Substrate: The organic material that you will be feeding your digester. This can be manure, plant waste, paper pulp, or other biodegradable material. |
2. Slurry: The slurry is the homogeneous mush that you will be passing through the digester. In order for efficient digestion to take place, the substrate material should be mashed or ground and mixed with water to make a uniform substance with 15 to 40% solids, depending on your digester design. |
3. Stratification: As your slurry breaks down in the digester, it will separate into layers. These layers — or “strata” — are biogas, scum, supernatant, sludge, and solids. Mixing of the slurry prevents excessive stratification, but some stratification will always occur, especially in “batch” digesters (see Micro-digester Designs: Global D.I.Y. Technology). |
4. Scum: The scum layer floats on the top of the material in the digester, just below the gas level. The scum level is formed by hard-to-digest material like coarse straw and grease. |
5. Supernatant: The spent liquid of the slurry. The Supernatant has a high content of solids, making it of high value as fertilizer, similar to “compost tea” (Diver, 2002). |
6. Sludge: Below the liquid supernatant is the sludge layer. The sludge is the digested and semidigested organic solids. This sludge can provide excellent composted fertilizer, but depending on the feedstock, it may need to be dried in the sun to kill any surviving pathogens. This is more of an issue with manure-based systems. |
7. (Inorganic) Solids or Sand: The bottom layer consists of those non-digestible solids that find their way into the digester. These could include dirt, sand, small rocks, plastic, or metal — any inorganic solid that may inadvertently be introduced into the system. |
Micro-Digester Designs: Global D.I.Y. (Do-It-Yourself) Technology
There are two basic types of digester designs: continuous-flow and batch processors. In a continuous-flow digester, new substrate is regularly fed into the digester. The slurry moves through the digester, pushing out digested material (effluent). The material may also be moved mechanically through the continuous-flow digester with augers or pumps. Batch digesters are loaded once and then the material is allowed to digest. When the digestion is complete, the effluent is removed and the process is repeated. By adding an inlet tube for feeding the digester and an outlet tube for the overflowing effluent, a batch processor can be fed some extra material after the initial start-up to extend the cycle, making the unit a semi-continuous batch processor. Each type has its advantages. Continuous digesters produce biogas without interruption. Batch digesters, on the other hand, are simpler and less expensive to build. Continuous-flow designs lend themselves better to manure-based systems, while batch processors may be more appropriate for unprocessed plant-based substrates.
The types of micro-digesters covered in this publication fall into three categories, with some variation: in-ground bag or tube style (continuous flow); in-ground dome style (semi-continuous batch); and floating top/tank design (batch or semi-continuous). Because much of the micro-scale biogas technology has been developed by individuals and non-governmental organizations, these designs are simple and “open source” — meaning that the designs are non-proprietary and much of the information on these designs is free and readily available on the Internet. (See the Resources section at the end of this publication for a list of books and websites to visit for more detailed information.)
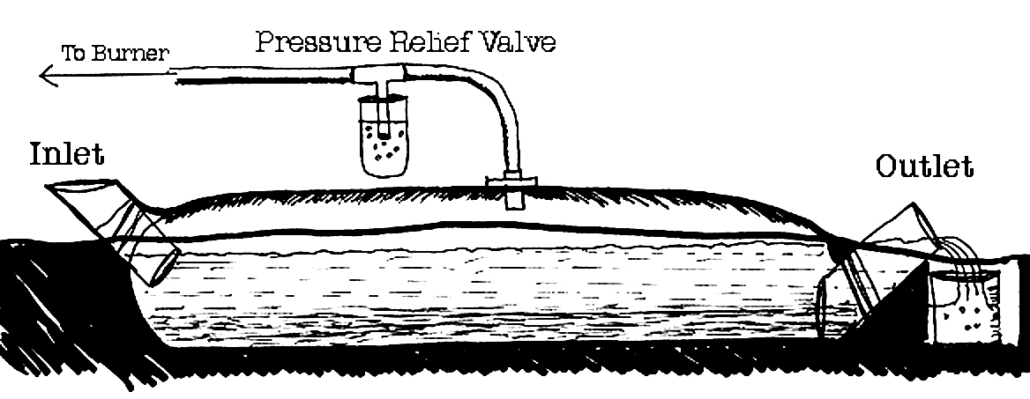
Figure 2. In-Ground Bag
In-Ground Bag
The in-ground bag style digester is very popular throughout Central America, and may be appropriate for use in the Southern U.S. It is a very simple continuous-flow design especially well-suited to a family farm with just a few pigs or cows. It is a very inexpensive design, with parts that can be acquired for as little as $50.
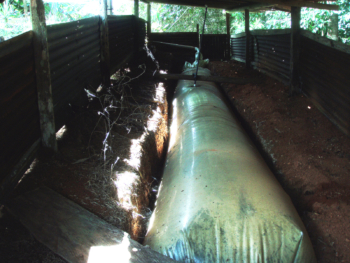
An in-ground bag digester in operation. Photo: Ian Woofenden
The system consists of a long trench (approx. 20 feet), lined with a 48 inch diameter polyethylene (poly) tube to form the “bag.” With an inlet at one end, an outlet at the other, and a gas outlet fitting on the top, it is an extremely simple design (see Figure 2). The poly tubing is available by the roll, and is commonly used as packaging material. A double layer of 6 to 8 mil poly is suggested to avoid punctures, and a pressure release allows excess gas to exit the system before over-inflation of the bag. This design will produce four hours of usable cooking gas per day and requires approximately 100 gallons of slurry to “charge” the digester, and an additional 10 gallons of slurry per day to maintain (Brown, 2004).
In-Ground Dome
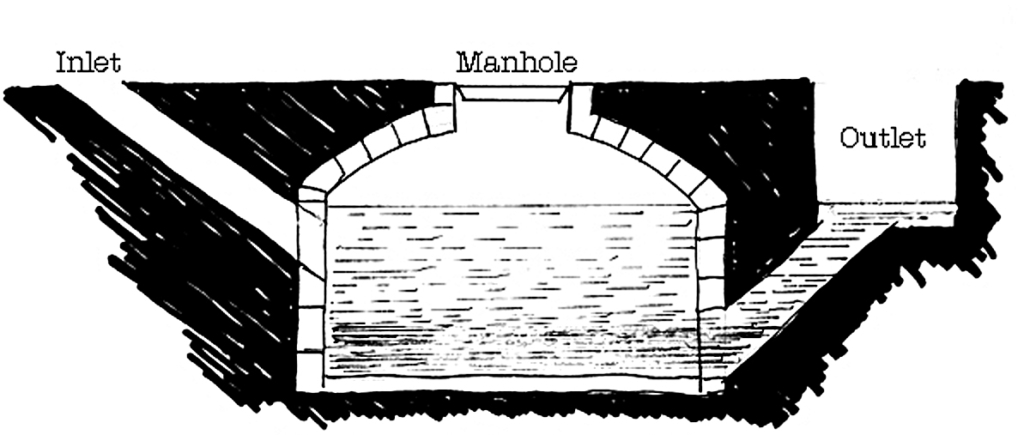
Figure 3. In-Ground Dome
The in-ground dome design is used widely in China and may have considerable potential for adaptation to northern climates in the United States (Koottatep et al., no date). This design is not unlike a western-style septic tank, and in fact, a conventional cast concrete or fiberglass septic tank could be modified to serve as a digester (see Figure 3). In China, the latrine is often connected to the digester, so it serves as a septic system as well. In the U.S., zoning and public health laws in most areas would not allow “blackwater” from the home into the digester, despite the obvious advantages of such a system.
This design involves a cast concrete or concrete block, or brick tank and cap. While the expense is much greater than that of a bag-style digester (typical cost is $350 for 4 to 6 cubic meters), but by using the earth’s natural insulation, the dome-style digester can maintain a constant temperature, even in colder climates (Nakagawa, 1981).
Floating Top/Tank
The floating top/tank design is one that adapts itself particularly well to the materials at hand. In this design, the slurry is contained in a bottom tank, with another inverted tank or drum serving as a cap, which is lifted by the biogas as it is generated (see Figure 4).
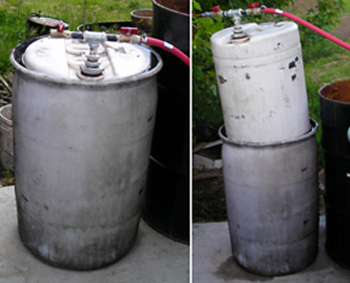
A simple floating-top digester built from scrap materials. Photo: Rich Dana, NCAT
This design is used widely in India in particular, where ARTI (Appropriate Rural Technology Institute) has developed a very functional family- sized design utilizing a 1,000-liter (264 U.S. gallons) polyethylene base tank with a 750-liter (198 U.S. gallons) tank as the inner floating gas chamber (Voegeli et al., 2009). This design can be adapted to use any size of tanks, with a larger diameter for the outer and smaller diameter for the inner tank, and can be an excellent and inexpensive design to experiment with. Many sizes of drums are readily available for free, and a very small test digester can be made with a couple of barrels and just a few standard plumbing parts (see Figure 4).
Other Designs
Several other designs have been developed that are variations on these three basic styles. One is a hybrid design that uses sealed, 55-gallon drums as modular digesters that are connected to a separate floating top/tank gas-storage container. Another style uses the 275-gallon totes commonly used to transport farm and industrial chemicals. In general, plastic containers are preferable to steel drums for the digester vessel and gas storage tanks, because both the slurry and the biogas itself can corrode steel drums fairly rapidly.
Start-Up, Operation, and Maintenance
Start-Up
The best way to get any anaerobic digester going is by “seeding” or “inoculating” it with material from another healthy, operating digester. Introducing live anaerobic bacteria into the new digester will expedite start-up, and the higher the ratio of inoculant material used, the more likely you will have a successful start-up. If only a small amount of seed material can be obtained, then new substrate should be added slowly over the course of several days to promote growth of the bacteria. If material from an existing digester is not available, active sludge from a sewage treatment plant can be used. Some DIY experimenters have used commercial septic tank treatments to promote start-up, but only anecdotal evidence is available on the effectiveness of using septic starter. Of course, some substrate material already contains anaerobic bacteria. Manure or material from the bottom of a compost pile will contain some anaerobic bacteria and will begin the process more quickly than will fresh vegetable or plant matter. In the case of manure, the fresher the better. Anaerobic material exists in the gut, and as it is exposed to air it begins to die. Dried dung will likely contain very little live bacteria.
A batch digester will generally be easier to start than a continuous flow unit because, for the latter, the hydraulic retention time (HRT) is less than in a batch digester. HRT is the time it takes for the slurry to move through the digester. In a continuous or semi-continuous flow arrangement, the digester should not be “fed” for several days after initial loading to allow the growth of the anaerobic bacteria. During this start-up period, pH should be monitored closely to make sure that the slurry is not slipping into an acid state. This can easily happen by adding new material too quickly. If the pH number begins to drop, lime or other “antacids” may be needed to keep the pH level in anaerobic operating range.
Operation and Maintenance
If a healthy environment is established for your anaerobic bacteria, very little effort is needed to operate a micro-digester. In a continuous-feed design, substrate should be added daily. A batch digester is loaded and then left alone (or agitated occasionally) until gas production falls below an acceptable level. In a small, continuous-flow digester, agitation occurs as the material is added and moves through the digester, although additional mechanical agitation can be added. Agitation of some kind is generally desirable because without it, depending on the substrate, a thick scum layer can form and hinder the gas production. Keeping substrate materials in suspension will assist in the uniform breakdown of the material and will promote complete digestion.
Loading the digester will be the most common operation, and this involves preparation of the slurry. Manure must be liquefied, food scraps must be mashed, cardboard or grasses must be shredded. Remember, the smaller the particles in your slurry, the happier your digester will be. How much you need to feed your digester is called the loading rate. The loading rate is derived from the amount of organic matter fed daily, divided by the size (volume) of the digester. A healthier anaerobic environment can handle a higher loading rate, but over-feeding the digester can cause a rise in the acid content and reduced gas production. Put more simply, more feedstock is not always better.
Cleanout is necessary when gas production drops below an acceptable level. This will be a regular occurrence in a batch digester but will be less necessary in a continuous-flow system, since much of the material will be leaving the system as effluent. In both cases, at some point during the operation, some digestate and inorganic solids will need to be removed.
Depending on the climate, heating the digester may be another consideration. Obviously, using any kind of fossil-fuel-based heating like propane, oil, or electricity doesn’t make economic or environmental sense, but it may be possible to use compost or solar heating, or to capture waste heat from another source, to keep a digester operating efficiently in the colder months.
A Word About Safety
Remember, at all stages of construction, operation, and maintenance of a digester, you are exposing yourself to potential hazards. Some feedstocks, especially manures, contain pathogens or parasites. You can be exposed to them not only in the loading phase, but also in clean-out, depending on retention times. The digestion process may not kill them all. In a dung-based system, special care should be taken to keep yourself, your tools, and your work area clean.
Methane and the other gases produced can be deadly. If you are a rural resident, you have probably heard stories of individuals who have been overcome by “septic gases” when cleaning a septic tank. The same can hold true for an anaerobic digester. Remember, the digester is designed to be an oxygen-free environment—good for anaerobic bacteria, bad for humans!
Finally, of course, biogas is explosive. Never smoke or use a torch or lantern in the presence of biogas, and use soapy water—NOT a flame—to test for the presence of biogas, unless it is fed to a properly regulated burner.
Gas Quality
Because biogas is coming fresh out of a warm, biological environment, a fair amount of water vapor is present in the gas. Systems for removing moisture will need to be implemented for good combustion. These can be as simple as pitching the gas pipe to cause the moisture to run back into the digester, or fashioning a moisture trap made out of a glass jar or bottle. Another potentially more serious issue is filtering or “scrubbing” the gas. Because of the corrosive nature of the hydrogen sulfide and ammonia in the raw biogas, pipes, burners, and especially generator engines can be damaged over time. A number of designs for scrubbers are available on the Internet, most using beakers or vessels packed with steel wool, or bubbling the gas through a solution of sodium carbonate.
Pressure
Achieving the proper pressure for combustion of the biogas can be done in several very simple ways. Rather than using a high-tech mechanical compressor, most people use the very low-tech method of adding weight to the top of the gas storage unit, using bricks or other heavy objects. This can be tricky with a bag digester, and care must be taken not to snag or puncture the plastic. Some trial and error is necessary, but in combination with a regulator valve and a carburetor orifice to adjust the gas/air mixture, a good, efficient flame can easily be achieved.
Environmental Benefits of Using Biogas
When biogas is burned, it does produce CO2, which is a greenhouse gas. However, using biogas is still environmentally beneficial. Along with CO2, methane is one of the greenhouse gases that concern scientists most in their study of global climate change. According to the U.S. Environmental Protection Agency (EPA), although there is less methane in the environment than CO2, methane is about 21 times more powerful at warming the atmosphere than CO2 (by weight). Methane’s chemical lifetime in the atmosphere is approximately 12 years (U.S. EPA, 2010). Burning the methane (rather than allowing it to escape into the atmosphere), using the energy and turning the emissions into CO2 reduces the potency of the greenhouse gases being released, but more importantly, displaces fossil fuel use and prevents the release of additional CO2.
The EPA estimates that in large-scale dairy digesters, for each 10 cows from which the manure is anaerobically digested and the biogas captured and used, greenhouse gas emissions are reduced an amount equivalent to taking 4.3 passenger cars off the road. Of course, this statistic does not address the overall lack of sustainability of large-scale confined animal feeding operations. Other sources estimate that small digesters can reduce greenhouse gas emissions by the equivalent of 5 to 7 metric tons of CO2 in households that currently burn wood (BMU, 2009).
Side Streams: Fertilizer and Compost Tea
Aside from biogas production, the other important benefit of operating an anaerobic digester is the high-quality fertilizer and compost that it produces. This side stream of the digester can provide your operation with a great deal of high-value soil amendments that can be used at the farm, or possibly sold for additional income. Certified organic producers should check with their certifiers for any restrictions.
The effluent and spent substrate that remain after anaerobic digestion contain higher concentrations of potassium, phosphorous, and nitrogen than the raw manure or plant waste that went into the digester. Unlike the raw feedstock, the nitrogen is more readily available to plants because it is now in a mineralized form, rather than an organic form.
In addition, weed seeds, parasites, and pathogens are much less of an issue than with raw manure. The temperature and lack of oxygen in the anaerobic environment is sufficient to destroy many weed seeds and pathogens. Nonetheless, particularly in the case of manure-based digesters, it is strongly advised that the spent substrate be sun-dried or composted before application to eliminate any possible surviving pathogens or parasites.
Conclusion
Building and operating a micro-scale biogas production system is not right for everyone. It can be messy and labor-intensive. Your regional climate, available feedstock, and ability to use the gas at your site will determine if a project is even viable. If you are looking for a good return on investment (ROI) in a conventional farm business model, it may be a hard case to make.
On the other hand, if you are a small-scale farmer looking to increase the sustainability of your operation by utilizing the resources at hand with an investment of “sweat equity” rather than cash, micro-scale biogas may be worth exploring.
References
Bates, L. 2007. Biogas Technical Brief. Practical Action. 7 p.
BMU—German Federal Ministry for the Environment, Nature Conservation & Nuclear Safety. 2009. Mini Biogas Plants for Households. Project number: 08_I_036_VNM_A_Biogas, 54 p.
Brown, Laura. 2004. Gas Bio-digester Information and Construction Manual for Rural Families. Sustainable Harvest International. 16 p.
Diver, Steve. 2002. Notes on Compost Teas. ATTRA Publication. National Center for Appropriate Technology. 19 p.
Fry, L. John. 1973. Methane Digesters For Fuel Gas and Fertilizer, With Complete Instructions For Two Working Models. The New Alchemy Institute. 58 p.
Fulford, David. 1988. Running a Biogas Program. Practical Action, Bourton on Dunsmore, UK. 200 p.
House, David. 2006. The Complete Biogas Handbook (3rd Edition). House Press. 288 p.
Koottatep, Suporn, Manit Ompont and Tay Joo Hwa. No date. Biogas: A GP Option For Community Development.
Nakagawa, Charles H. 1981. Chinese Biogas Digester. U.S. Peace Corps Information Collection and Exchange. 92 p.
U.S. EPA. 2010. Methane.
Voca, N. et al. 2005. Digester residue as fertilizer after mesophilic process of anaerobic digestion. Faculty of Agriculture, University of Zagreb, Croatia. 265 p.
Voegeli, Y., C. Lohri, G. Kassenga, U. Baier and C. Zurbrugg. 2009. Technical and Biological performance of the ARTI compact biogas plant for kitchen waste. CISA Publisher, Italy. 9 p.
Woofenden, Ian. 2009. Appropriate Technology for the Developing World. Home Power Magazine. Oct./Nov. 80 p.
Micro-Scale Biogas Production: A Beginners Guide
By Rich Dana
IP370
Slot 369
Version 082910
This publication is produced by the National Center for Appropriate Technology through the ATTRA Sustainable Agriculture program, under a cooperative agreement with USDA Rural Development. ATTRA.NCAT.ORG.