An Introduction to Bioenergy: Feedstocks, Processes, and Products
By Leif Kindberg, NCAT Farm Energy Specialist
Abstract
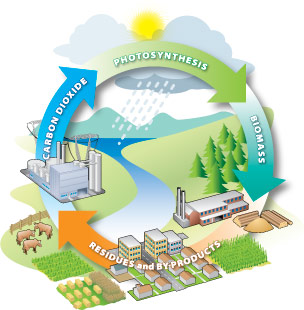
Carbon cycling is the foundation of sustainable bioenergy. Source: BC Bioenergy Strategy
Bioenergy offers farmers an alternative to petroleum-based energy sources and new market opportunities for farm products. When biomass feedstocks are burned, fermented, or reacted through an energy-conversion process, they return some carbon dioxide and water and release the sun’s energy. Because plants have the capability to store and then release energy in this way, they act as a natural battery. This introduction to bioenergy offers a brief and non-technical overview of bioenergy feedstock production with discussion on how bioenergy is made.
Introduction
Bioenergy uses renewable biomass feedstocks from many sources. Renewable biomass feedstocks use the process of photosynthesis in plants to capture the sun’s energy by converting carbon dioxide (CO2) from the air and water (H2O) into carbohydrates and complex oil and fiber compounds made up of carbon, hydrogen, and oxygen. These energy-rich carbohydrates, oils, and fibers can be harvested and used for many types of bioenergy. There are hundreds of ways to turn biological materials into energy, although currently only a few of them represent legitimate short-term opportunities for the average farm or rural landowner.
Bioenergy was used in industrial processes well before petroleum and coal-fired electricity were commonly available. Although a great deal of attention goes to solar and wind energy, bioenergy BTUs (British thermal units of energy) generated from biomass make up 53 percent of all renewable energy in the United States, according to the Energy Information Administration. That is more than all other renewable sources combined (EIA, 2009). However, bioenergy presents a complex set of energy topics. This publication will discuss many of these complex topics but will only mention others. Topics that will not be discussed in any detail in this introductory publication include most feedstock pre-processing considerations such as transporting, sizing, drying, and storage.
Feedstock Basics
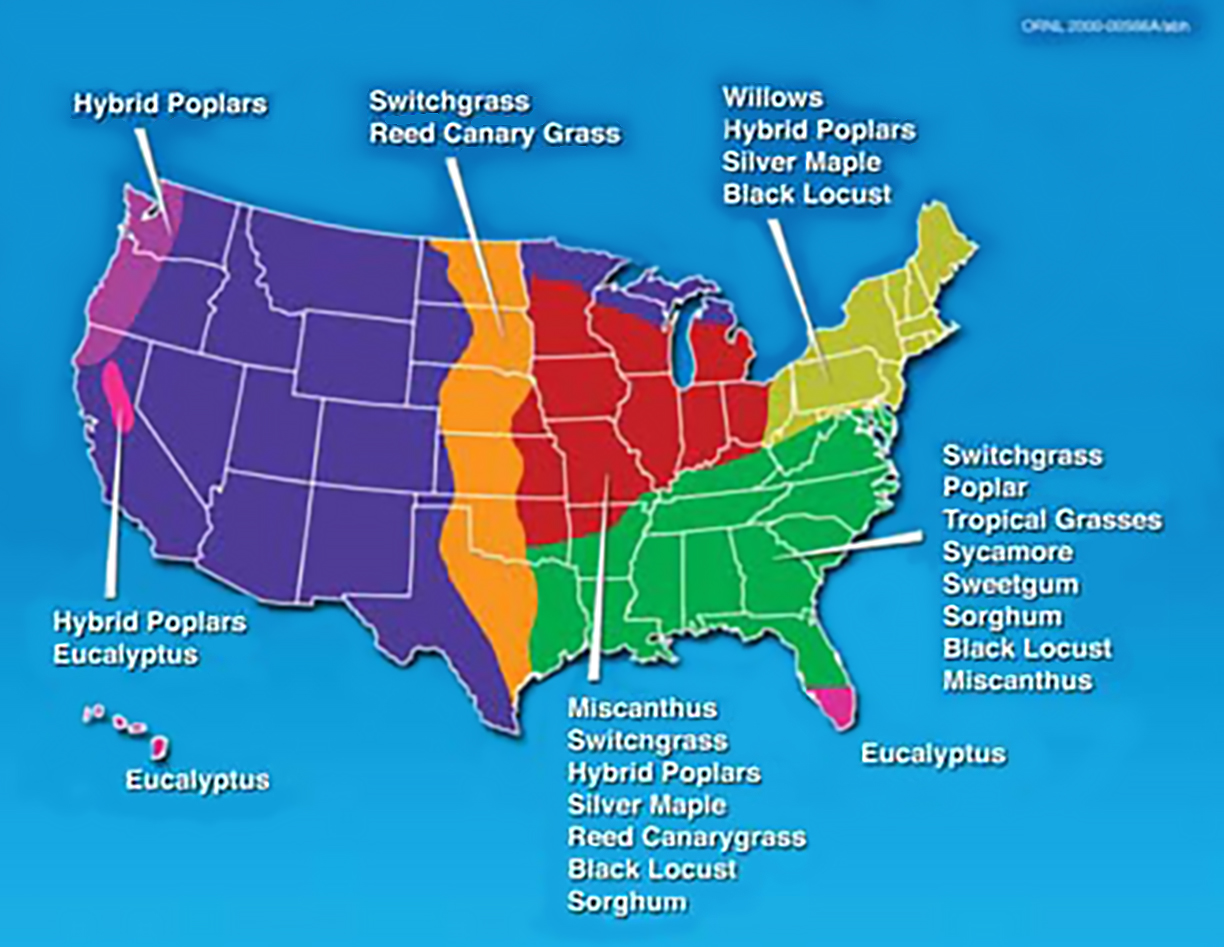
The geographic range of some bioenergy crops. Source: ORNL
Bioenergy can be produced from feedstocks such as trees, agricultural crops, plant residues, animal parts, and many other biological materials. The benefits of one feedstock versus another are regionally specific. This makes feedstock selection a key consideration in bioenergy production.
Feedstocks may be dedicated to energy production or non-dedicated. Feedstocks that are dedicated are often called energy crops. Each feedstock has advantages and disadvantages that may include how much usable biomass they produce, soil types required, water and energy inputs, energy density, air-quality benefits, production cost, and other considerations.
Sugar and Oil Feedstocks
Sugar and oil feedstocks often include seeds, grains, and plants that are made up of sugar, starch or oil, and animal fats or tallow. Today, these feedstocks are often used to produce the biodiesel and ethanol fuels we are familiar with.
Sugar Feedstocks
The two most common bioenergy feedstocks used for their starch and sugar content are corn and sugar cane. Over 90 percent of ethanol (or bioethanol as it is sometimes called) is still made from corn in the United States. The world’s largest producer of ethanol is Brazil. Brazil uses sugar cane as its primary feedstock. Because fermentation produces alcohols, the higher the yield of fermentable sugars in the feedstock, the higher the yield of alcohols. Since fermentation can process almost any starch into sugar, other feedstocks may include barley, milo, wheat, potatoes, sugar beets, cheese whey, brewery and beverage waste, and many others. Many of these feedstocks serve multiple functions as either food or fuel sources.
Oilseed Feedstocks
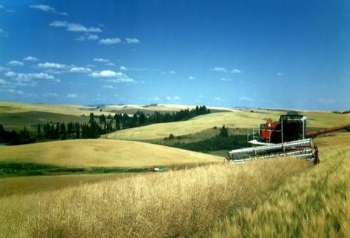
Canola (rapeseed) being harvested for oil. Photo: NREL
Plants that have oil-rich seeds, frequently referred to as oilseeds, can be a sustainable source of bioenergy. Common American oilseed crops include soybeans, canola, sunflower, camelina, safflower, and cottonseed. Camelina is a short-season crop that is well-suited for double cropping and grows well in cooler climates such as the northern Midwest. In comparison, many varieties of sunflower are well-suited for warmer Southern climates. Canola (one cultivar of rapeseed) is particularly well-suited for cooler regions, with varieties that are adapted for both spring and fall planting to achieve multiple oilseed harvests. Your state agricultural experiment station, Cooperative Extension Service, or the Natural Resources Conservation Service (NRCS) may have information on specific oilseed crops that are well-adapted to your location and information on the best rotations for soil-building, water needs, and pest management. See the ATTRA publication Biodiesel: The Sustainability Dimensions for more information about oilseed feedstocks.
Cellulosic Feedstocks
Feedstocks from cellulose (the primary component in the cell walls of plants) such as poplars, willows, and switchgrass are creating a lot of excitement among farmers, scientists, and the public. These fibrous and generally inedible parts of plants are abundant and can be collected from diverse regions or grown directly by farmers. Although there is currently a very limited market for cellulosic bioenergy feedstocks in the United States, some companies are currently purchasing cellulosic biomass for pellets and for cofiring (burning biomass with coal). A few companies intend to begin commercial production of cellulosic ethanol. Demand for cellulosic biomass is expected to expand market opportunities in the near future.
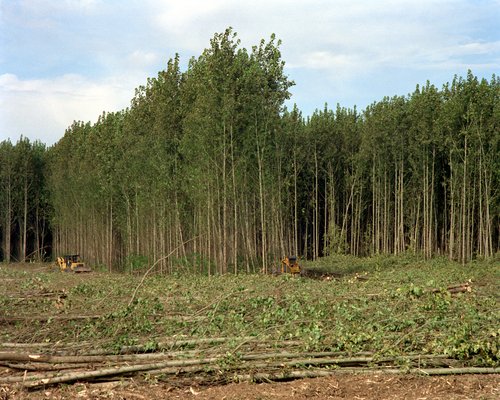
Short-rotation hybrid poplar trees. Photo: NREL
Energy crops can be grown on farms using practices similar to those used with other agricultural crops. Trees and grasses, particularly those that are native to a region, can be sustainably produced when grown with minimal inputs such as water, fertilizer, and chemicals. Trees that will regrow after each harvest may be coppiced (repeatedly cut off at ground level), allowing them to be harvested multiple times. Woody varieties that regrow quickly without being replanted are called short-rotation woody crops. Perennial varieties of grasses and legumes are also being tested and used as feedstocks. Many energy crops are being researched for their bioenergy potential.
Agricultural Residues
Residues left over from forest products and farming may also be used as cellulosic feedstocks. The U.S. Department of Energy has estimated that between 581 and 998 million dry tons of agricultural residues such as corn stover and wheat straw (the stalks and leaves left on a field after a harvest) could be harvested for biofuels by the middle of the 21st century (DOE, 2005). However, research has also shown that less than 25 percent of some agricultural residues could be sustainably harvested under current agriculture practices because crop residues are critical to soil fertility (Graham et al., 2007). Study results vary widely on the quantity of agricultural residues that may be sustainably harvested. What is certain is that when left in the field, agriculture residues help restore soil tilth, protect agricultural soils, and sequester carbon. The removal of agricultural residues is unlikely to be sustainable unless agricultural best management practices such as cover crops, no-till production, and better fertilizer management are fully adopted, among other practices (Marshall and Zugg, 2008).
Animal Manure
Manure is used for feedstocks in anaerobic digesters primarily to produce gas burned to generate electricity. Although there are substantial environmental and welfare issues associated with confined animal feeding operations, these large operations are increasingly using manure digestion to control a variety of environmental problems, reduce odors, generate bioenergy for the farm, and provide additional income through the sale of power.
The Production of Bioenergy
Feedstocks require a conversion process in order to take raw materials and turn them into useful bioenergy such as electricity, biodiesel, ethanol, biobutanol, methane, heat, and other bioenergy products. Keep in mind that harvesting, drying to the correct moisture content, transporting to the necessary location, and supplying a sufficient quantity of biomass are important considerations that are only briefly mentioned in this introduction to bioenergy. Each type of feedstock may require a slightly different conversion process, but many feedstocks can be converted using similar processes and technologies.
Thermochemical Conversion
Heating biomass assists a chemical reaction (a thermochemical process) and creates useful bioenergy products such as gases, liquids, and heat. Electricity generated from biomass is referred to as biopower, and the combination of both heat and power is commonly referred to as cogeneration or combined heat and power (CHP). The overall efficiency of these integrated systems is significantly higher than either of the systems alone.
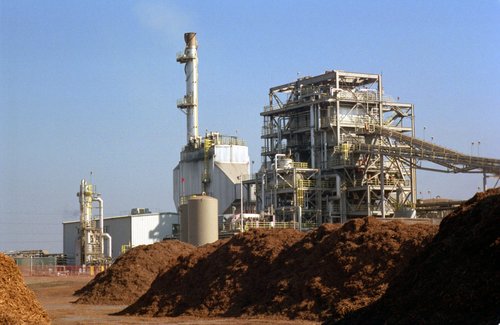
This 21-megawatt direct-fired biopower plant uses wood residues discarded from orchards and industrial operations. Photo: NREL
Combustion in a Direct-Fired or Conventional Steam Boiler
The burning of feedstocks for energy has been practiced for many years. One of the oldest commercial methods of producing electricity is through the burning of wood or charcoal to produce steam. The steam is piped into a turbine that spins a generator used to make electricity, or biopower. A problem with burning feedstocks in a steam boiler is that a great deal of energy is lost in the conversion process. Pre-processing biomass by pelletizing, torrefaction (superheating in a low-oxygen environment), or making condensed biomass briquettes has helped improve the efficiency of burning woody biomass. These processes are expensive and not always economical given current fossil fuel prices.
Cofiring
Cofiring woody biomass and high-fiber grasses with coal can reduce carbon dioxide emissions compared to burning coal alone. Many plant-based feedstocks have lower sulfur contents than coal, reducing sulfurous gases including sulfur dioxide. Cofiring plant-based feedstocks has been successfully demonstrated to replace up to 20 percent of the coal used in the boiler, according to the Federal Energy Management Program (2004). However, the economics of cofiring have generally not been favorable with historical fossil fuel prices. You should carefully consider the market opportunities in your local area if you are planning to produce feedstocks for cofiring, and you should pursue long-term supply contracts.
Thermal Process Heat and Space Heat
Burning biomass directly can be used to produce both process heat and space heat. Process heat is vital to many manufacturing processes and is used in a variety of agricultural applications including grain and crop drying. Space heating is the most common use. Both large boilers in manufacturing facilities and small stoves in shops are frequently used for space heat. Wood, wood chips, and hay can be used for both process heat and space heat, and are readily available on the farm.
Thermal Gasification
Gasification converts feedstocks into combustible gases called synthesis gas (syngas) that can be used to produce heat, motor fuels, biopower, chemicals, and for other purposes. Syngas is also sometimes referred to as producer gas, wood gas, and town gas. Synthesis gases are generally upgraded to other fuel products such as ethanol, methanol, hydrogen, and ammonia using processes such as the Fischer-Tropsch process. These fuels and process will be discussed later in this publication. Gasification occurs at temperatures generally between 1,202 and 1,832 degrees Fahrenheit (650 to 1,000 degrees Celsius) and deliberately limits burning in order to convert feedstocks into useful intermediates to be used as energy later (Sadaka, 2010). Gasification exposes the feedstock to some oxygen, but not enough to allow the feedstock to burn. The conversion efficiency of gasification systems is high, typically between 80 and 85 percent efficiency in taking a raw feedstock and converting it into producer gas (NREL, no date). Controlling the temperature, pressure, feedstock characteristics, and other aspects changes the energy density and makeup of the producer gas.
More on gasification can be found on the Sun Grant BioWeb website, a non-commercial, educational website that provides current information about biomass resources for bioenergy and bioproducts.
Pyrolysis
Pyrolysis is derived from the Greek words pyro, meaning fire, and lysys, meaning decomposition. Pyrolysis is a method of producing syngas and biocrude, also known as bio-oil or pyrolysis oil. Pyrolysis uses thermal decomposition by heating biomass at temperatures usually greater than 400 degrees F (204 degrees C). Biocrude is formed when syngas produced during pyrolysis is re-condensed into liquid biocrude. There are few opportunities to use unrefined biocrude directly on the farm and a limited market. Biocrude can be refined into high-quality hydrocarbon fuels such as diesel, gasoline, and jet fuel. These liquid fuels can be used in internal combustion engines as a chemically identical substitute to petroleum fuels.
Pyrolysis is often the first process that occurs during the burning of solid fuels including wood. Pyrolysis releases gases that are visible as yellowish and orange flames. If you were to stop burning these gases and condense them, you would have a form of biocrude. Next, the solids (charcoal) left behind are burned but have no visible flame. Instead of letting these solids burn, they can be converted into biochar. Using modern pyrolysis for energy stops the burning of both gases and solids short. |
Pyrolysis variables such as temperature, pressure, reaction rates, and other factors produce a wide variety of gas, liquid, and solid intermediates. However, generally pyrolysis processes with higher temperatures and more rapid reaction rates are most efficient at producing biocrude. The pyrolysis process known as fast or high-temperature pyrolysis has higher reaction rates (greater than 1,000 degrees F or 538 degrees C). This process can be used to optimize biocrude or char production. Low-temperature pyrolysis processes are generally used to produce char. Pyrolysis and gasification are both complex processes that require laboratory-like conditions to consistently produce bioenergy products.
Biochar is a type of charcoal that is high in organic carbon and is a coproduct of pyrolysis of biomass. Char has many potential benefits in agriculture (International Biochar Initiative, no date). Biomass pyrolysis systems for biocrude and biochar production are available in smaller demonstration units at this time, but some larger-scale facilities are being built.
For more information on biochar, see the ATTRA publication Biochar and Sustainable Agriculture. More on pyrolysis can be found on the Sun Grant BioWeb website.
Fischer-Tropsch Process
The Fischer-Tropsch process converts syngas usually produced during gasification into unrefined liquid fuels such as biocrude. The Fischer-Tropsch process usually takes place in a pressurized and high-temperature environment. This process chemically converts a gas generally composed of carbon monoxide and hydrogen into liquid fuels or oils that can then be burned in an internal combustion engine and used to make other fuels. Fischer-Tropsch liquids can be refined further into hydrocarbon fuels such as gasoline and diesel and used as a direct replacement for petroleum-derived fuels.
Haber-Bosch Process
The Haber-Bosch process is a synthesis reaction between nitrogen gas, hydrogen gas, and an iron catalyst. The Haber-Bosch process is often used in sequence with steam reforming of natural gas or coal into gaseous hydrogen to produce ammonia. The entire process of producing ammonia is often referred to as the Haber-Bosch process.
Gaseous hydrogen for the Haber-Bosch process can be produced using electricity from wind, solar, water, biomass, and other renewable resources. Instead of using natural gas or coal to produce hydrogen, biopower is used to electrolyze water and produce hydrogen. This offers the benefit of releasing fewer carbon dioxide emissions, but has normally required large amounts of energy and remains cost-prohibitive because of low-cost natural gas and coal.
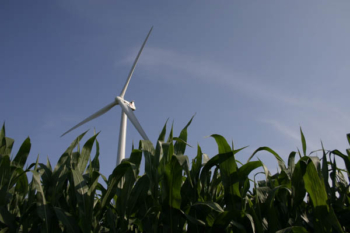
Wind electricity may be used to electrolyze water and produce hydrogen, a key component of ammonia. Photo: University of Minnesota Renewable Energy Center
Ammonia
Ammonia produced during the Haber-Bosch process can be run in modified internal combustion engines as an alternative liquid fuel. Ammonia has about half the energy of gasoline and can be generated from a variety of renewable energy sources. Farmers who have experience with ammonia application know there are many hazards associated with the handling and use of ammonia. The broad use of ammonia as a liquid fuel for vehicles will require substantial investments in safe storage and handling, and require improvements in transportation infrastructure.
Methanol
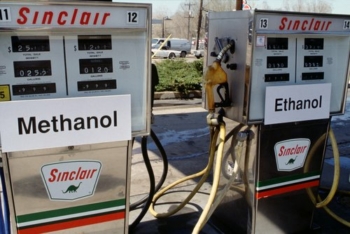
Methanol and ethanol pumps. Photo: NREL
Methanol or wood alcohol is usually produced from methane during steam-methane reforming of natural gas and coal. Methane produced from anaerobic digestion of manure (discussed next) may also be an option but is usually cost-prohibitive. Methanol can be used as a substitute for gasoline with some engine modifications but has only about half the energy density of gasoline. Methanol can also be converted into synthetic fuels such as dimethyl ether (DME) to be used as a diesel substitute with significantly lower emissions and with about half the energy density of diesel. Methanol is already commonly used in the transesterification process of producing biodiesel, which is discussed.
Biochemical Conversion
Bacteria, yeasts, and other living enzymes ferment material such as sugars and proteins and convert them into useful alcohols or other liquid fuels. These processes are known as biochemical conversion processes. Corn ethanol and other grain alcohols are some of the most common fuels produced in this way. Other methods include capturing methane produced when bacteria break down manure from livestock and poultry production, human sewage, and landfill waste to burn it for heat and biopower.
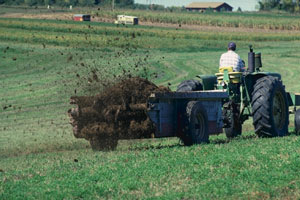
Anaerobic digestion creates a variety of nutrient-rich liquids and solids that can be used on the farm. Photo: USDA ERS
Anaerobic Digestion
Anaerobic digesters break down (or digest) organic matter without oxygen (anaerobic) to produce methane and other gases and coproducts that are useful on the farm. This gas mixture is commonly referred to as biogas or digester gas. Biogas is a combustible and normally consists of 50 to 60 percent methane. Biogas can be burned in an engine to generate biopower and thermal energy or processed further into other fuel types such as methanol. Refined biogas can be used as compressed natural gas (CNG) and liquefied natural gas (LNG) in automobiles, among other uses. The byproducts from anaerobic digestion can be used as soil amendments and liquid fertilizers. For more information, see the ATTRA publication Anaerobic Digestion of Animal Wastes: Factors to Consider.
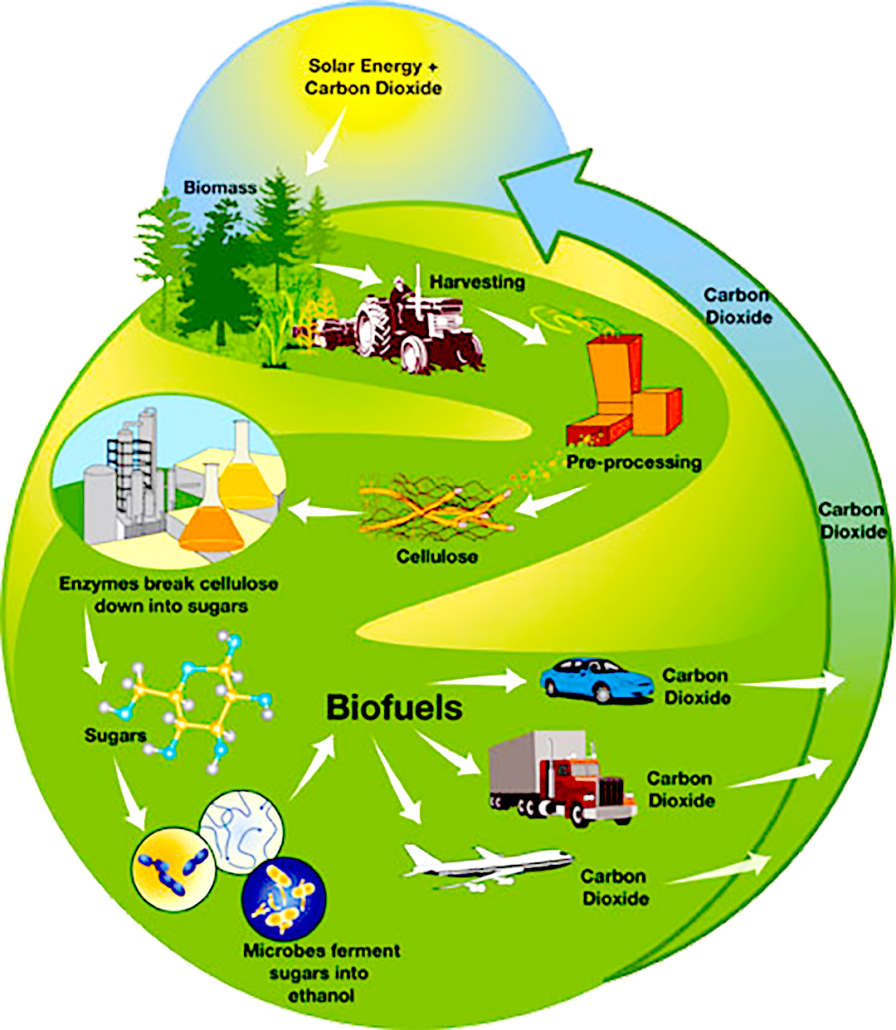
Cellulosic biofuels and the carbon cycle. Source: US DOE
Fermentation (for Ethanol)
Ethanol, a fuel alcohol, is made from biological sources and usually is produced through the fermentation of plant starches and sugars. In the United States, corn is the most common source of starch converted into ethanol, while barley, milo, wheat starch, potatoes, cheese whey, and brewery and beverage waste make up a smaller share of production. Ethanol can also be produced from sugarcane, which has a high content of the sugars needed for fermentation. According to the Renewable Fuels Association, the United States produced 9 billion gallons of ethanol in 2008 and 22 million metric tons of distillers grains were sold from the ethanol making process (2008).
Ethanol from corn and other grains can be made using either a dry-milling or a wet-milling process. The dry-milling process uses the whole corn kernel, which is ground into a powder, mixed with water to form a mash, and then cooked with added enzymes that turn the liquefied starch to glucose (sugar). After cooling, the mash is fermented with a second enzyme (yeast) and finally distilled further to separate the alcohol from the solids and water. Coproducts of the dry milling process include distillers grain, which is used as animal feed (also known as distillers dried grain with solubles or DDGS) and carbon dioxide.
The wet-milling process involves soaking the corn kernel in water and sulfurous acid before grinding the kernels into a mash. This soaking separates the germ (oil), fiber, gluten (protein), and starch components. The starch is fermented into ethanol and then distilled further, corn oil is extracted from the germ, and both fiber and other starch components are separated. While dry-milling provides valuable coproducts such as DDGS, the wet-milling process is also used to produce corn oil, corn gluten, and meal.
As with ethanol produced from starch grains, processing cellulosic feedstock for ethanol aims to extract fermentable starch from the feedstock. However, the starches found in cellulose are hard to extract because they are locked in complex carbohydrates called polysaccharides (long chains of simple sugars). To produce ethanol from cellulose efficiently, these chains of simple sugars must be broken up prior to fermentation. Fermenting sugars from cellulose into ethanol is less efficient than fermenting sugars directly, although ethanol from either source is chemically identical.
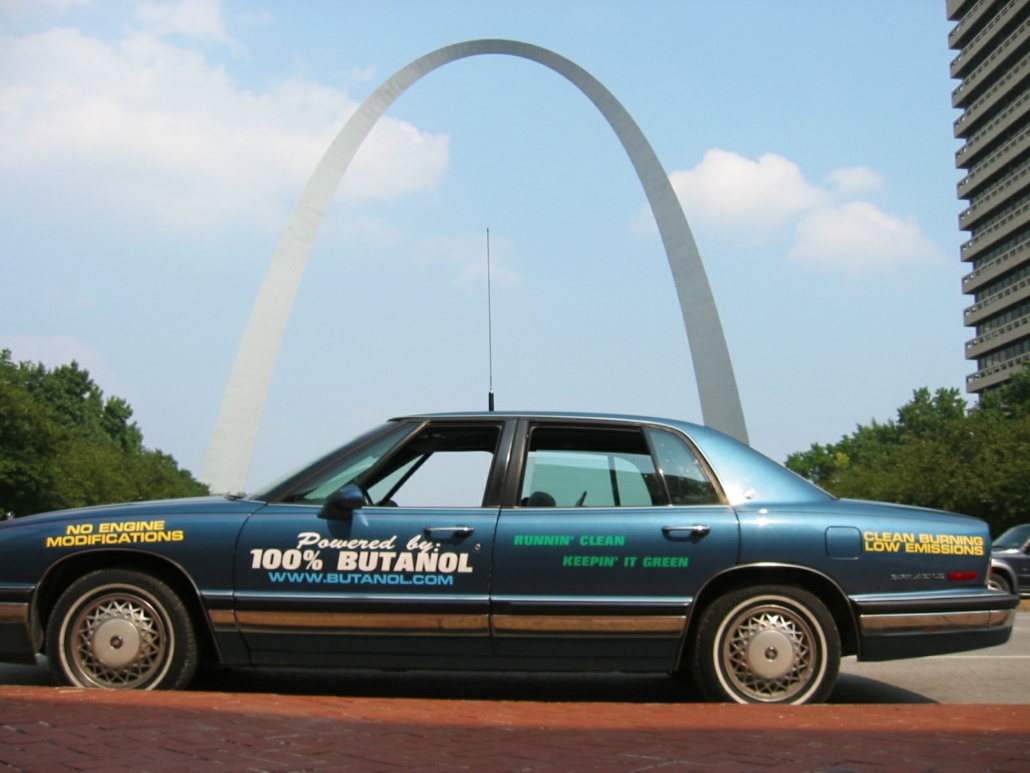
A ButylFuel vehicle was driven across the United States on 100 percent biobutanol. Photo: ButylFuel, LLC
The conversion of cellulose to sugar is generally accomplished through one of two processes. The first uses acid hydrolysis (a method of splitting water molecules) to break complex carbohydrates into simple sugars. The second uses a combination of pre-treatment to break apart the feedstock cell structure and enzymatic hydrolysis for the production of fermentable sugars. Cellulosic ethanol may also be produced from gasification, which is a thermochemical process.
Biobutanol
Biobutanol is very similar to gasoline and is produced in much the same way as ethanol. Biobutanol is produced by Acetone-butanolethanol (ABE) fermentation. Biobutanol has an energy density that is 10 to 20 percent lower than gasoline and slightly higher than ethanol. The Environmental Protection Agency allows biobutanol to be blended with gasoline up to 11.5 percent. Higher blends have greater restrictions and may require modifications to internal combustion engines (DOE, no date). Biobutanol can be delivered to the end user with existing pipeline and storage infrastructure in many cases. However, biobutanol is toxic to humans and is water-soluble, which means it may easily find its way into water sources.
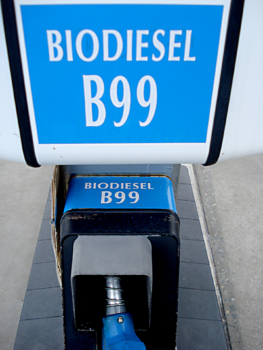
Biodiesel is blended with petroleum-based diesel to produce B99 and lower blends. Photo: Leif Kindberg
Transesterification for Renewable Diesel Fuels
Transesterification is a chemical process that reacts an alcohol with the triglycerides contained in vegetable oils and animal fats to produce biodiesel and glycerin. This process is commonly used to produce B100 biodiesel, or 100-percent biodiesel to be blended with petroleum diesel. Biodiesel is essentially permanently thinned plant oil or animal fat, with a viscosity approximating that of standard No. 2 petroleum-based diesel fuel. Biodiesel is chemically different from petroleum-based diesel because it contains oxygen atoms and is not a pure hydrocarbon. For more information about biodiesel, see the ATTRA publication Biodiesel Use, Handling, and Fuel Quality.
Another type of renewable diesel known as green diesel or hydrogenation-derived renewable diesel is more like petroleum-based diesel, but uses many of the same plant oil and animal fat feedstocks used in making biodiesel. Green diesel is produced using a chemical reaction known as hydrocracking or hydrotreating. Hydrocracking is a process in which hydrogen is added to organic molecules under pressure and heat. An important advantage of green diesel is that it can be produced as a chemically identical replacement to petroleum diesel.
Straight Vegetable Oil (SVO)
The viscosity (thickness) of straight vegetable oil may cause buildup when burned in an unmodified engine. However, engines that burn straight vegetable oil are available and modification kits are available as well. With the correct filtering, heating, and conversion of a diesel engine, straight vegetable oil offers a partial alternative to bio-based or No. 2 petroleum-based diesel fuel. For more information about straight vegetable oil, see the ATTRA publication Biodiesel Use, Handling, and Fuel Quality.
An important part of bioenergy production is the net energy balance (also referred to as the energy balance). The energy balance is a life cycle method of accounting for the amount of energy needed to make a unit of bioenergy versus the amount of usable energy produced. Therefore, the life cycle energy balance of bioenergy will include inputs required to plant, cultivate, fertilize, harvest, transport, dry, and process the feedstock and convert it into a useful bioenergy form. Said another way, the energy balance is the difference between the energy produced and the energy needed to produce that given unit of energy.
The complexity involved in accurately calculating the energy balance of bioenergy makes the calculations almost impossible to conduct at this point. The methods used to produce an energy crop on one farm, for example, may be somewhat or significantly different on the next. An example of this could be intercropping nitrogen fixers and perennial grasses without the use of herbicides on one farm versus using alternative nutrient and weed-management practices on the next farm. |
Conclusion
Through its role in the carbon cycle, bioenergy can reduce direct emissions such as carbon dioxide (CO2) when compared with petroleum- based energy. For example, when biomass feedstocks are grown, they pull carbon dioxide from the air and make stems, roots, leaves, and seeds. When biodiesel from oilseeds is burned, carbon dioxide and other emissions are released back into the air and are taken up again by next year’s energy crop, thus completing the carbon cycle. In comparison, when fossil fuels such as coal or petroleum-based fuels are burned, all of the carbon dioxide released adds additional carbon dioxide into the air (NREL, 2008). However, not all bioenergy is equally good at reducing emissions. There are many complex factors to consider when thinking about biomass and bioenergy production on the farm.
Some things to consider include:
- Is there a local market for my feedstock or fuel or can I use it on the farm to offset energy costs?
- Will the quantity of fertilizer and energy used during the production of my feedstock be positive or negative for the environment?
- Will converting my land, once out of agricultural production, into production (indirect land-use change) create additional greenhouse gases?
- How much energy will be consumed during transportation of feedstocks?
- How much energy will be used during feedstock conversion?
- Will bioenergy provide net positive benefits to my farm and the environment when all the economic, energy, and environmental costs are added up?
This publication did not provide answers to all these questions and is meant as a starting point for learning about bioenergy. It is not a complete reference guide and you are encouraged to explore all of the additional publications and resources provided by ATTRA and in the Further Resources that follow.
Further Resources
Bioenergy Feedstock and Production Resources
For a glossary of bioenergy terms see Energy.gov Bioenergy Technologies Office Glossary.
The Alternative Fuels and Advance Vehicles Data Center provides information on the production, distribution, and benefits of biobutanol, biodiesel, ethanol, hydrogen, methanol, natural gas, propane, ultra-low sulfur diesel, biogas, p-series fuels, and much more.
Journey to Forever is a small, non-government organization based in Japan and involved in Third World rural development work. The website also offers a lot of information about biofuels and other appropriate technologies.
The Sun Grant BioWeb provides both non-technical and technical information on biomass, bioenergy conversion technologies, biomass economics, and related policy.
The Center for Bioenergy Information is a helpful gateway to biomass resources from the U.S. Department of Energy, Oak Ridge National Laboratory, Idaho National Laboratory, National Renewable Energy Laboratory and other research organizations.
The Agricultural Marketing Resource Center provides resources on value-added agriculture including bioenergy feedstocks.
The National Renewable Energy Lab (NREL) is a learning resource covering biofuels, biopower, bioproducts, and other energy technologies for farms and ranches.
Additional Online Resources
International Biochar Initiative
U.S. Department of Energy — Energy Efficiency and Renewable Energy
Roundtable on Sustainable Biofuels
An Introduction to Bioenergy: Feedstocks, Processes and Products
By Leif Kindberg, NCAT Farm Energy Specialist
©NCAT
IP359
This publication is produced by the National Center for Appropriate Technology through the ATTRA Sustainable Agriculture program, under a cooperative agreement with USDA Rural Development. ATTRA.NCAT.ORG.